How can wear and corrosion issues in the Injection machine barrel screw be mitigated, and what maintenance measures can be taken?
Mitigating wear and corrosion issues in an injection machine barrel screw is crucial for maintaining performance and extending the lifespan of the equipment. Here are some strategies and maintenance measures:
Mitigating Wear Issues:
1.Material Selection: Opt for high-quality materials with superior wear resistance properties, such as nitrided steel or bimetallic alloys.
Conduct a thorough analysis of material characteristics and operational requirements to ensure compatibility with processing conditions.
2.Surface Treatments: Apply advanced surface treatments, including nitriding, hard chrome plating, or tungsten carbide coatings, to enhance the hardness and wear resistance of the barrel screw.
Collaborate with reputable coating specialists to choose the most suitable treatment based on the specific processing environment.
3.Optimized Processing Conditions: Implement a comprehensive process optimization strategy by fine-tuning parameters such as temperature, pressure, and screw speed.
Employ advanced monitoring and control systems to prevent deviations in processing conditions that could contribute to accelerated wear.
4.Regular Inspection: Institute a regular inspection regimen to detect early signs of wear, including dimensional changes, surface roughness variations, or material buildup.
Utilize precision measurement tools and non-destructive testing methods to assess wear patterns and identify potential areas of concern.
5.Proper Material Handling: Institute stringent material handling protocols to minimize the introduction of contaminants or abrasive particles.
Implement comprehensive training programs for machine operators to ensure adherence to proper handling practices.
Mitigating Corrosion Issues:
1.Material Compatibility: Conduct a comprehensive material selection process, considering factors such as corrosion resistance, when choosing barrel screw materials.
Collaborate with material suppliers to acquire detailed information on the chemical compatibility of selected materials with various plastic resins.
2.Barrel Coatings: Invest in high-performance coatings or liners with proven corrosion resistance properties.
Engage with coating experts to determine the most suitable coating material based on the specific corrosive elements present in the processing environment.
3.Material Drying: Establish and enforce stringent material drying procedures to eliminate moisture content before introducing hygroscopic materials into the processing system.
Integrate moisture monitoring systems to ensure the effectiveness of the drying process.
4.Purge Compounds: Implement a systematic purging routine using specialized compounds designed to cleanse the barrel and screw surfaces.
Collaborate with purging compound manufacturers to select products that are tailored to the specific resin types being processed.
Maintenance Measures:
1.Regular Cleaning: Develop and implement a routine cleaning schedule that addresses both preventive and corrective maintenance needs.
Utilize approved cleaning agents and procedures to remove contaminants without compromising the integrity of the barrel screw.
2.Barrel Inspections: Conduct thorough visual inspections, utilizing endoscopes or similar tools, during scheduled maintenance intervals.
Record and analyze inspection data to track wear trends and make informed decisions regarding refurbishment or replacement.
3.Screw Inspection: Establish a comprehensive screw inspection protocol, including dimensional checks and material integrity assessments.
Collaborate with original equipment manufacturers (OEMs) or certified refurbishment services for in-depth screw evaluations and refurbishment.
4.Temperature Control: Institute robust temperature control measures to prevent overheating and thermal degradation.
Implement advanced temperature monitoring systems with automated controls to maintain precise and uniform temperatures throughout the barrel.
Injection machine barrel screw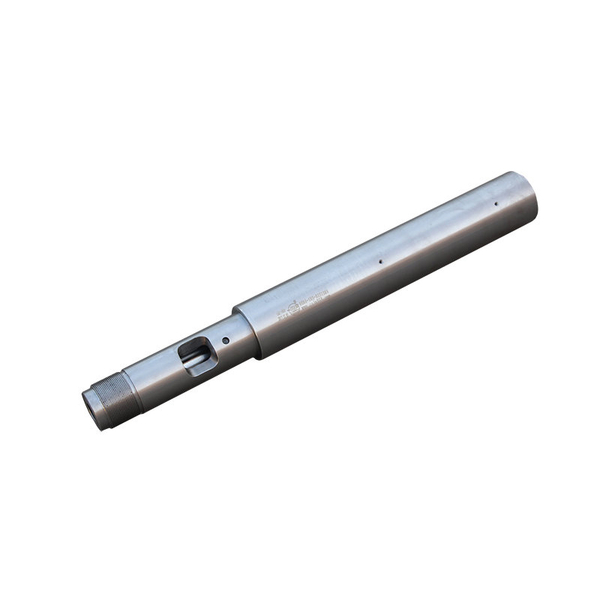