How does the design of the Conical twin screw barrel impact the efficiency of the extrusion process?
The design of the Conical twin screw barrel plays a crucial role in determining the efficiency of the extrusion process. Here are several factors related to its design that impact efficiency:
Enhanced Mixing and Homogenization: The Conical twin screw barrel employs strategically placed mixing zones with specialized screw elements to create an environment of intense material interaction. This design promotes not only mechanical mixing but also distributive mixing, ensuring a thorough blending of additives and polymers. The enhanced homogenization achieved through precise control over the mixing process results in a final product with consistent properties, meeting the stringent quality requirements of various industries.
Increased Length-to-Diameter Ratio: The remarkable length-to-diameter ratio of Conical twin screw barrels provides an extended processing path, allowing for a nuanced approach to material transformation. As the material progresses through the elongated barrel, it undergoes multiple stages of conveying, melting, and pressurization. This extended residence time enhances the opportunity for controlled reactions, facilitating a more efficient extrusion process that accommodates the intricacies of diverse materials and formulations.
Varied Screw Element Configurations: The adaptability of Conical twin screw barrels is exemplified by the diverse configurations of screw elements that can be strategically placed along the barrel. This customization allows operators to fine-tune the extrusion process based on the specific requirements of the material. Whether optimizing conveying efficiency, promoting efficient melting, or achieving precise mixing, the ability to vary screw element configurations ensures versatility in processing a wide range of materials with distinct characteristics.
Temperature Control: Conical twin screw barrels excel in temperature control through the incorporation of multiple independently controlled heating and cooling zones. This sophisticated temperature management system enables operators to maintain precise control over material temperatures at different sections of the barrel. The meticulous control of temperature is essential, particularly when processing temperature-sensitive materials, ensuring optimal conditions for efficient extrusion without compromising the material's structural integrity.
Reduced Shear Stress: The Conical geometry is designed to address the challenge of shear stress, a critical consideration when dealing with heat-sensitive materials. By minimizing shear stress through the carefully engineered geometry, the Conical twin screw barrel ensures a controlled and gentle treatment of the material. This reduction in shear stress not only preserves the integrity of the material but also contributes to a more predictable and efficient extrusion process.
Optimized Melting and Compression: The Conical twin screw barrel optimizes the melting process by incorporating a controlled heating profile along the barrel. This gradual and precise heating prevents overheating or degradation, ensuring efficient material melting. Additionally, the tapering diameter towards the discharge end enhances material compression. This controlled compression is crucial for achieving thorough densification of the melt, promoting efficient material processing and contributing to the overall extrusion efficiency.
Versatility in Processing Multiple Materials: Conical twin screw barrels are celebrated for their versatility in accommodating an extensive range of materials with varying viscosities and formulations. The adaptable design enables seamless processing of different materials within a single extrusion line. This versatility not only streamlines manufacturing processes but also offers operational flexibility, allowing manufacturers to respond dynamically to changing material requirements across different industries.
Conical twin barrel screw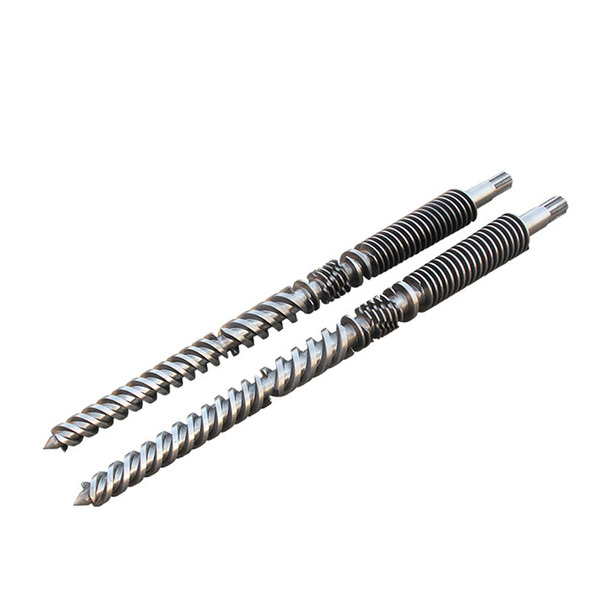