How does the screw geometry influence the residence time and shear rate of the material in the barrel?
The screw geometry plays a critical role in determining both the residence time and shear rate of the material in the barrel of an injection molding machine. Here's how:
Flight Depth: Flight depth is a fundamental aspect of screw geometry that profoundly influences material flow dynamics within the barrel. The distance between the outer diameter of the screw and the inner diameter of the barrel dictates the volume of material that can be accommodated along the screw's channel. This volume directly impacts residence time, as a larger flight depth allows for a greater quantity of material to be conveyed per revolution of the screw. Consequently, the material spends more time within the barrel, undergoing processes such as melting, mixing, and homogenization. Longer residence times are particularly advantageous for achieving uniform properties in the final molded parts, as they facilitate thorough blending of additives, colorants, or recycled materials with the base resin. However, excessive flight depth may lead to prolonged residence times, risking material degradation or overheating, especially for heat-sensitive polymers.
Pitch: The pitch of the screw, defined as the distance between adjacent flights along its length, directly influences material displacement and, consequently, residence time. A longer pitch results in greater material conveyance per revolution of the screw, effectively increasing the throughput rate and extending residence time. This prolonged residence time offers several advantages, including enhanced mixing and homogenization of the material, which are critical for achieving consistent melt properties and part quality. Longer residence times can improve the incorporation of additives or fillers, ensuring uniform distribution throughout the melt. However, it's essential to consider the trade-offs associated with longer pitches, such as potential increases in energy consumption or shear-induced degradation. Conversely, shorter pitches reduce material displacement per revolution, leading to shorter residence times. While this may be desirable for minimizing material exposure to high temperatures or reducing cycle times, it can also compromise melt quality and mixing efficiency.
Compression Ratio: The compression ratio of the screw, expressed as the ratio of the feed zone depth to the metering zone depth, profoundly impacts material processing within the barrel. A higher compression ratio increases the pressure and temperature of the material as it progresses along the screw, effectively prolonging residence time. This extended residence time enables more extensive melting, mixing, and homogenization of the material, resulting in improved melt quality and part consistency. The elevated pressure promotes better compaction and densification of the melt, reducing voids or inconsistencies in the final molded parts. However, excessive compression ratios may lead to overworking of the material, causing degradation, discoloration, or excessive energy consumption.
Channel Depth: The depth of the screw channels, which refers to the space between adjacent flights, significantly influences material conveyance and residence time. Deeper channels accommodate a larger volume of material, facilitating increased material transport along the screw's length and, consequently, extending residence time. This prolonged residence time allows for more thorough mixing, blending, and thermal processing of the material, leading to enhanced melt quality and part performance. Deeper channels promote better engagement between the screw and the barrel, minimizing leakage or bypassing of unmelted material. However, excessively deep channels may impede material conveyance or increase shear forces, potentially leading to processing challenges or premature wear of the screw.
Injection machine screw
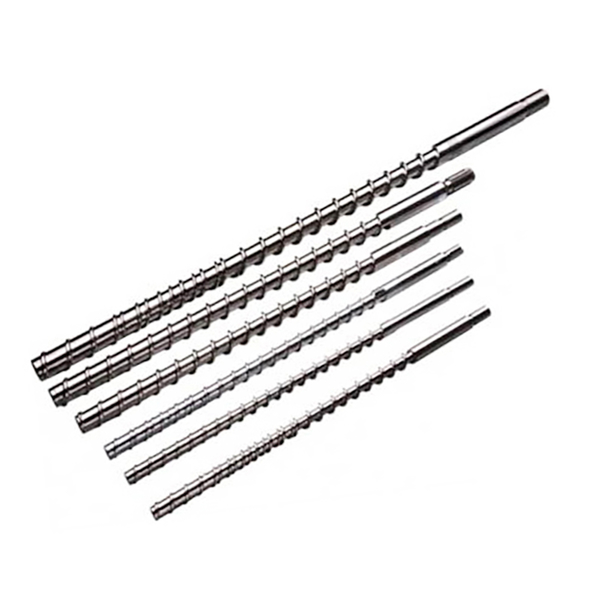