What safety features are integrated into the conical twin screw barrel design to prevent overheating or other operational risks?
Safety features in conical twin screw barrel designs aim to prevent overheating and mitigate operational risks. Some common safety features include:
Temperature Monitoring Systems: Implementing a robust temperature monitoring system involves deploying a network of high-precision sensors and thermocouples strategically along the entire length of the conical twin screw barrel. These sensors, calibrated for accuracy, continuously relay real-time temperature data to a centralized control system. This not only allows for precise monitoring but also enables the establishment of temperature profiles along the barrel. In the event of any deviation from the optimal range, the system can execute a rapid and automated shutdown, preventing not only overheating but also ensuring the consistency of thermal conditions critical for precise material processing.
Cooling Systems: The integration of cooling systems goes beyond mere heat dissipation. Advanced water or air cooling mechanisms are engineered to adapt dynamically to the extrusion process demands. Variable cooling rates and targeted cooling zones are designed to maintain a delicate balance between preventing overheating and avoiding unnecessary cooling that may impact material properties. The cooling infrastructure, complemented by smart control algorithms, actively contributes to thermal management, minimizing thermal stress on the barrel and auxiliary components.
Thermal Insulation: Selecting and applying thermal insulation materials involves a meticulous process. High-performance insulating materials, chosen for their thermal resistance and durability, are precisely fitted to the barrel. The insulation serves a dual purpose by not only preventing external surfaces from reaching hazardous temperatures but also by enhancing energy efficiency. This professional-grade insulation contributes to the overall thermal stability of the extrusion system, ensuring that the heat generated during the process is effectively contained and utilized.
Emergency Stop Mechanism: The emergency stop mechanism is engineered with redundancy and failsafe features. The design incorporates high-reliability switches or buttons strategically located for immediate accessibility. These components are intricately linked to a failsafe control system that, in the event of an emergency stop activation, orchestrates a swift and controlled shutdown sequence. This professional approach ensures that the emergency stop mechanism is not only responsive but also reliable, preventing unintended triggers and facilitating a quick recovery to normal operation after the emergency has been resolved.
Pressure Relief Devices: Pressure relief devices are precision-engineered components that serve as a critical safety net for pressure management. These devices, often calibrated to specific pressure thresholds, employ sophisticated valve systems. In the event of pressure spikes within the barrel, the valves open strategically to release excess pressure safely. Professional design considerations encompass the choice of materials for these devices, ensuring compatibility with the processed materials and minimizing the risk of leakage or malfunction. Regular testing and calibration schedules are established to guarantee the ongoing effectiveness of these pressure relief mechanisms.
Automatic Venting Systems: Automatic venting systems are designed with a deep understanding of the volatile nature of certain materials processed in conical twin screw extruders. Professional-grade venting systems incorporate precise sensors and actuators that respond dynamically to variations in material characteristics. The venting process is not only automatic but also optimized for efficiency, ensuring that volatile substances are expelled promptly and safely. These systems are engineered to prevent any accumulation of potentially hazardous materials within the barrel, eliminating the associated risks of pressure buildup and ensuring a controlled extrusion environment.
Conical twin barrel screw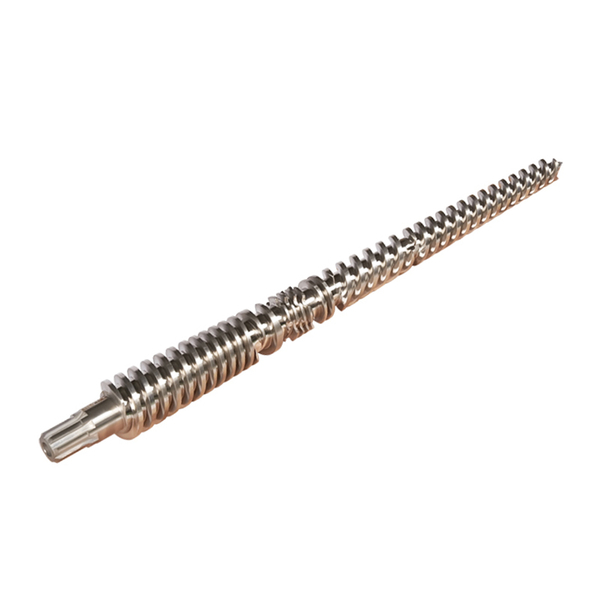