How do you control the film thickness and width in a double die film blowing machine?
Controlling the film thickness and width in a double die film blowing gadget is vital for producing notable films that meet particular necessities. Here's how movie thickness and width are generally managed in such machines:
1.Die Design Optimization:
Engineers meticulously layout the die geometry, considering factors which include die hole, land duration, and access/go out angles. Finite element analysis and computational fluid dynamics are frequently hired to ensure uniform flow distribution and minimal fabric distortion. Precise die design is crucial for attaining the preferred film thickness and width.
2.Die Gap Adjustment:
Operators can exceptional-track the die hole, the gap between the die lips, to reap the focused film thickness. This adjustment is made primarily based at the specific polymer houses, processing conditions, and the favored cease-product specifications. Continuous monitoring and adjustment of the die hole are vital at some point of operation to preserve regular movie thickness.
3.Screw Speed Control:
The rotational velocity of the extruder screw directly influences the output charge of the molten polymer. By adjusting the screw pace thru the device's control panel, operators can exactly manipulate the volume of fabric extruded in line with unit of time. Maintaining a constant screw velocity is important for controlling both movie thickness and width.
4.Extruder Temperature Management:
The extruder barrel is geared up with heating and cooling zones. Proper temperature manipulate inside these zones is important. Heating ensures the resin reaches the desired viscosity for extrusion, at the same time as cooling prevents overheating and degradation. Temperature sensors and control systems regulate the barrel temperatures as it should be, making sure the cloth's viscosity remains within the most suitable range for the preferred movie dimensions.
5.Cooling Rate Optimization:
After extrusion, the film passes via cooling structures, which include air jewelry or water baths, to solidify the cloth. The cooling fee must be cautiously controlled to save you choppy cooling, that may cause versions in film thickness and width. Uniform cooling guarantees the movie keeps its dimensions continuously as it solidifies.
6.Bubble Cage or IBC System Integration:
Some advanced movie blowing machines include a Bubble Cage or Internal Bubble Cooling (IBC) machine. These systems use adjustable air stress to keep a stable bubble shape. By carefully regulating the air pressure at special points, operators can manipulate the movie's width and thickness, specifically inside the case of multi-layer films wherein particular layer distribution is important.
7.Thickness Measurement and Control Devices:
Inline thickness size gadgets, such as beta or gamma ray sensors, ultrasonic gauges, or laser-primarily based sensors, constantly reveal the movie thickness as it is being extruded. Real-time remarks from those sensors allows the manage gadget to make instantaneous adjustments, along with die hole or screw speed modifications, making sure that the movie adheres to the desired thickness necessities.
8.Automatic Control Systems and Industry four.0 Integration:
State-of-the-artwork double die film blowing machines are often ready with sophisticated computerized manage systems and Industry 4.Zero technologies. These structures use statistics analytics, gadget gaining knowledge of algorithms, and real-time comments loops to optimize technique parameters. Through predictive analysis, these structures can expect deviations and proactively adjust settings to hold regular movie thickness and width, thereby improving performance and minimizing waste.
LDPE One Screw Double Die Film Blowing Machine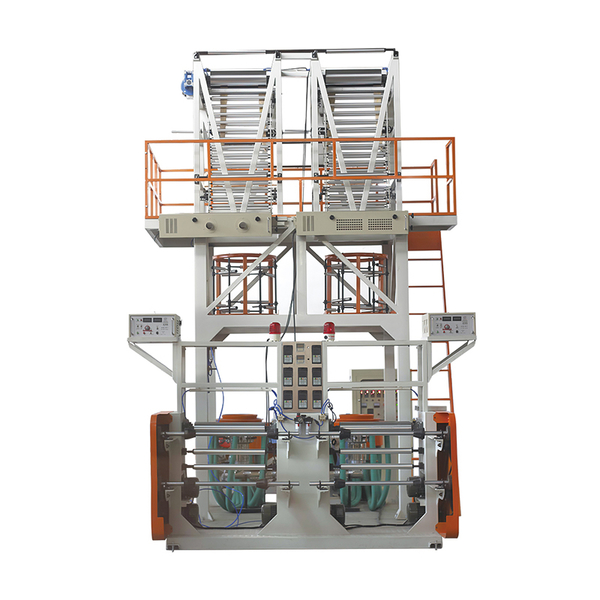