What measures can be taken to minimize wear and abrasion on a double-vented pelletizing screw during operation?
Several measures can be implemented to minimize wear and abrasion on a double-vented pelletizing screw during operation:
Material Selection: Carefully evaluate the mechanical properties of potential materials for the pelletizing screw, considering factors such as hardness, toughness, and corrosion resistance. Engage in thorough material testing to ensure compatibility with the abrasive characteristics of the processed polymers. Seek advice from material engineers to identify the most suitable alloy or composite for enhanced wear resistance.
Surface Coatings: Explore advanced surface coating technologies to augment the wear resistance of critical screw components. Delve into the specifics of each coating option—such as chemical composition, deposition methods, and thickness—to tailor the coating to the unique wear patterns experienced by the double-vented pelletizing screw. Collaborate with coating specialists to ensure proper adhesion and uniform coverage.
Hardening Treatments: Engage metallurgical experts to implement heat treatment processes that optimize the balance between surface hardness and core strength. Perform rigorous testing to validate the effectiveness of hardening treatments in real-world pelletizing conditions. Fine-tune the heat treatment parameters to achieve the desired hardness profile and minimize the risk of brittleness.
Optimized Design: Employ state-of-the-art design methodologies, including finite element analysis (FEA) and computational fluid dynamics (CFD), to optimize the screw geometry. Collaborate closely with design engineers to understand the flow characteristics of the polymer melt and tailor the screw design to minimize wear-prone areas. Iteratively refine the design through simulation and prototyping.
Regular Maintenance: Institute a comprehensive maintenance program that encompasses scheduled inspections, thorough cleaning, and lubrication of critical components. Develop detailed checklists for maintenance personnel, specifying key wear indicators to monitor. Implement predictive maintenance techniques, such as vibration analysis and thermography, to detect potential issues before they escalate.
Cooling Systems: Integrate advanced cooling systems that provide precise temperature control along the entire length of the pelletizing screw. Collaborate with thermal engineers to optimize the cooling system design, ensuring efficient heat dissipation. Implement real-time temperature monitoring and feedback mechanisms to maintain the screw within the optimal operating temperature range.
Melt Filtration: Collaborate with filtration experts to design and implement a robust melt filtration system. Select filtration media with the appropriate mesh size and filtration efficiency to capture contaminants effectively. Regularly monitor and replace filtration elements to prevent clogging, which can exacerbate wear. Consider implementing automated filtration monitoring systems for real-time performance evaluation.
Optimized Processing Parameters: Work closely with process engineers to establish a comprehensive understanding of the polymer processing parameters. Conduct systematic experiments to identify the optimal combination of melt temperature, pressure, and screw speed for minimizing wear. Implement closed-loop control systems to maintain process parameters within tight tolerances.
Proper Pelletizing Conditions: Collaborate with die and cutting mechanism specialists to optimize pelletizing conditions. Utilize advanced die designs that distribute stress evenly across the screw. Implement precision cutting mechanisms with hardened blades and automated adjustment capabilities. Regularly inspect and maintain these components to ensure consistent pelletizing conditions.
Material Consistency: Institute stringent quality control measures for raw materials, collaborating with material suppliers to establish and maintain material specifications. Implement real-time material testing and monitoring to detect variations in material properties. Establish clear communication channels with material suppliers to address any deviations promptly.
Double-vented pelletizing screw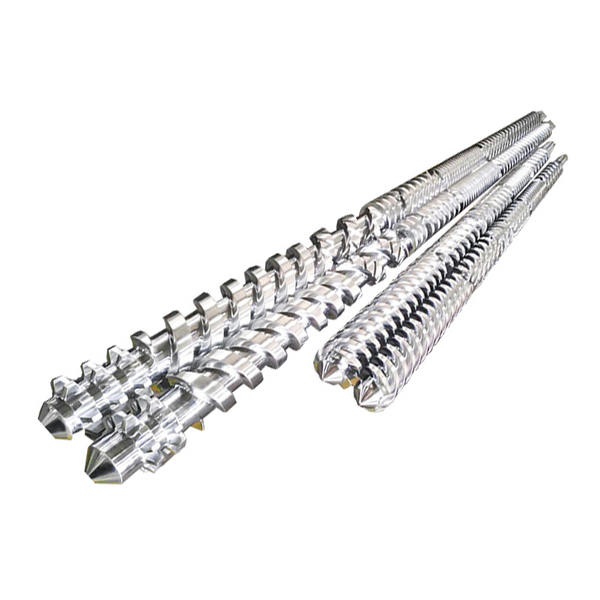