How does the geometry of the conical twin screw barrel affect the mixing and homogenization of materials?
The geometry of the conical twin screw barrel plays a crucial role in the mixing and homogenization of materials in several ways:
Channel Depth and Width: The dimensions of the channels between the screw flights are critical determinants of the shear rate experienced by the materials. Narrow channels increase shear rates, promoting more intense mixing and dispersion. This effect is particularly significant for viscous materials or those containing additives or fillers with a tendency to agglomerate. The geometry must be finely tuned to balance channel dimensions to achieve the desired level of shear without causing excessive pressure build-up or material degradation.
Screw Pitch: Screw pitch governs the axial movement of materials along the barrel and profoundly influences mixing kinetics. A tighter pitch increases the number of shear events experienced by the materials per unit length, promoting more thorough mixing. However, excessively tight pitches can lead to increased frictional heating and shear stress, potentially compromising material integrity or causing melt degradation. Optimal pitch selection involves a nuanced understanding of material rheology, processing conditions, and desired mixing objectives, often informed by empirical testing and rheological analysis.
Screw Configuration: The strategic incorporation of various mixing elements along the screw flights facilitates different mixing mechanisms and enhances overall mixing efficiency. Kneading blocks induce intensive shear and elongational forces, promoting distributive and dispersive mixing. Reverse elements disrupt material flow patterns, enhancing distributive mixing by promoting interfacial contact between material layers. Distributive mixing elements create chaotic flow patterns, maximizing interfacial area and promoting thorough mixing.
Barrel Taper: The taper angle of the conical twin screw barrel significantly impacts material residence time and flow behavior. A steeper taper increases residence time by reducing the cross-sectional area available for material flow, promoting more extensive mixing and interaction between materials. However, excessively steep tapers may lead to material stagnation or uneven flow distribution, necessitating careful optimization to balance mixing efficiency and material throughput.
Temperature Control: Precise temperature control mechanisms integrated into the barrel play a critical role in regulating material viscosity and flow behavior, thereby influencing mixing efficiency. Heating elements facilitate material melt and viscosity reduction, promoting flow and dispersion, particularly for thermoplastic materials. Conversely, cooling elements prevent overheating and material degradation while maintaining desired processing temperatures, crucial for heat-sensitive materials or reactive formulations. Advanced temperature control systems, such as PID (Proportional-Integral-Derivative) controllers and thermocouple arrays, enable precise regulation of barrel temperature profiles, optimizing mixing performance and ensuring consistent product quality.
Barrel Length: Barrel length directly impacts material residence time and the number of mixing stages within the processing zone. Longer barrels provide increased residence time and additional opportunities for mixing, facilitating sequential processing steps such as premixing, dispersion, and final homogenization. However, excessive barrel length may lead to unnecessary energy consumption and residence time distribution issues, necessitating careful consideration of processing objectives and material characteristics.
Conical twin barrel screw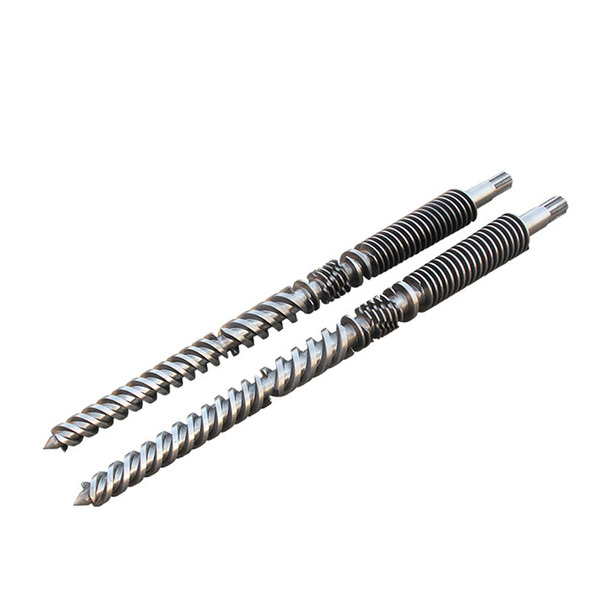
Material nature:38CrMoALA
Hardness of accent nature:HB260-290
Depth of nitration:0.40-0.70mm
Hardness of the surface:Hv90o-1050
Roughness of the surface:Ra0.32um
Linearity of the screw:0.015mm/m