How does the torque distribution along the length of the parallel twin screw barrel affect the extrusion process and product uniformity?
The torque distribution along the length of the parallel twin screw barrel plays a crucial role in the extrusion process and product uniformity. Here's how it affects them:
Material Conveyance: Torque distribution governs the rotational force exerted on the screws, which directly influences material conveyance along the barrel. Even torque distribution ensures consistent material flow rates, preventing areas of stagnation or material hang-ups that could disrupt the extrusion process. Uneven torque distribution might lead to localized pressure variations, resulting in material compaction or degradation. This can particularly affect materials with varying viscosities or additives, where consistent flow is crucial for maintaining product integrity and quality.
Mixing and Homogenization: Uniform torque distribution is pivotal for achieving thorough mixing and homogenization of the material melt. It ensures that additives, fillers, and other components are uniformly dispersed throughout the extrudate. Effective mixing is critical for achieving desired material properties, such as color consistency, mechanical strength, and thermal stability. Inadequate mixing due to uneven torque distribution can lead to material inconsistencies, resulting in defects or performance issues in the final product.
Temperature Control: Torque distribution directly impacts the generation and dissipation of heat within the barrel. Consistent torque distribution promotes uniform heating along the barrel length, maintaining precise control over melt temperatures and viscosity. This is essential for controlling material flow characteristics, melt homogeneity, and final product dimensions. Non-uniform torque distribution may lead to localized overheating or cooling, resulting in temperature variations that affect material properties and processing behavior.
Pressure Build-up: Uniform torque distribution ensures even pressure distribution within the barrel, which is crucial for stable extrusion conditions. Consistent pressure levels promote uniform flow rates and product dimensions, minimizing variations in extrudate properties. In contrast, uneven torque distribution can cause pressure fluctuations, leading to instabilities in the extrusion process. This can result in defects such as surface imperfections, dimensional inaccuracies, or product inconsistencies, impacting product quality and performance.
Energy Efficiency: Optimal torque distribution maximizes energy efficiency by minimizing energy losses associated with frictional resistance. Even torque distribution ensures smooth operation of the extruder, reducing the energy required to overcome frictional forces. This results in lower energy consumption and operating costs, contributing to overall process sustainability. Conversely, non-uniform torque distribution may lead to localized energy losses, requiring additional energy input to compensate for inefficiencies, thereby increasing operational expenses.
Screw Wear: Torque distribution influences the wear patterns experienced by the screws and barrel surfaces during operation. Even torque distribution promotes uniform wear along the screw flights and barrel bore, extending the service life of the equipment. This ensures consistent material processing conditions over time, maintaining product quality and dimensional accuracy. Non-uniform torque distribution can cause uneven wear, leading to irregularities in screw geometry or barrel surface, which may compromise extrusion performance and necessitate premature equipment maintenance or replacement.
Control of Residence Time: Torque distribution affects the residence time distribution of the material within the barrel, influencing material processing characteristics and product properties. Uniform torque distribution ensures consistent residence times for all material particles, facilitating uniform material treatment and processing. This results in consistent product quality and performance. In contrast, non-uniform torque distribution may lead to variations in residence time, causing material degradation or uneven processing, which can manifest as defects or inconsistencies in the final product.
Flat double barrel screw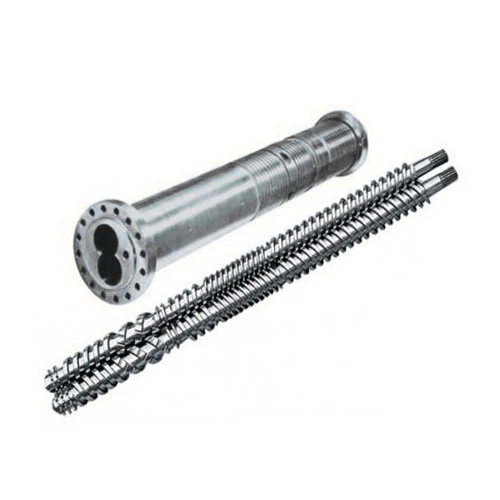