In what ways do parallel twin-screw barrels contribute to energy efficiency, and what measures can users take to optimize energy consumption in their processes?
Parallel twin-screw barrels can contribute to energy efficiency in various ways, and users can implement certain measures to optimize energy consumption in their processes. Here are key aspects to consider:
Enhanced Mixing and Dispersion: The inherent advantages of parallel twin-screw barrels lie in their ability to achieve both distributive and dispersive mixing with remarkable efficiency. This dual mixing capability substantially reduces the processing time needed to attain material homogeneity. In applications where thorough blending of additives, fillers, or colorants is crucial, the parallel twin-screw design offers a distinct advantage in minimizing energy consumption while ensuring uniformity throughout the material.
Improved Melting and Conveying: The design of parallel twin-screw barrels plays a pivotal role in promoting effective material melting. The configuration provides an increased surface area for material contact and optimizes shear rates, resulting in a more efficient melting process. This, in turn, translates to a significant reduction in the energy required to achieve the desired melt viscosity. Furthermore, the enhanced conveying efficiency of the parallel twin-screw extruder reduces material resistance, contributing to energy savings by facilitating smoother material flow and reduced torque demands.
Barrel Cooling Systems: The careful engineering of barrel cooling systems serves as a critical aspect of energy efficiency in parallel twin-screw extruders. By maintaining optimal processing temperatures, these systems prevent excessive heat generation during the extrusion process. This not only ensures the integrity of the processed materials but also minimizes the need for additional energy to compensate for overheating. A well-regulated cooling system is, therefore, a cornerstone of sustainable energy practices in extrusion processes.
Screw Speed Optimization: The versatility of parallel twin-screw extruders extends to the ability to optimize screw speed strategically. This adjustment capability allows operators precise control over shear rates and residence times, tailoring the extrusion process to the specific requirements of the material being processed. The result is a finely tuned, energy-efficient operation that aligns with the principles of responsible resource utilization without compromising the quality or characteristics of the final product.
Efficient Drive Systems: The integration of energy-efficient drive systems, such as variable frequency drives (VFDs), represents a technological leap in optimizing energy consumption in parallel twin-screw extruders. These systems empower operators to dynamically adapt the extruder's speed based on real-time processing demands. By aligning energy consumption with operational needs, VFDs contribute to a significant reduction in wasted energy, supporting a more sustainable and economically viable production environment.
Process Monitoring and Control: The implementation of advanced process monitoring and control systems provides users with real-time insights into energy usage patterns during extrusion processes. This data-centric approach enables proactive identification of inefficiencies, allowing for timely adjustments to optimize energy consumption. By fostering a culture of continuous improvement and data-driven decision-making, these systems contribute not only to energy efficiency but also to overall process optimization and product quality.
Insulation: The judicious application of insulation across the entire extrusion system, including barrels, represents a pragmatic approach to minimizing heat losses. Proper insulation mitigates the dissipation of heat, reducing the demand for additional energy to compensate for thermal inefficiencies. This meticulous approach to thermal management not only enhances the energy efficiency of the extrusion process but also underscores a commitment to sustainable manufacturing practices.
Material Selection: The nexus between material science and energy efficiency is evident in the strategic selection of raw materials for the extrusion process. Opting for materials with lower melt temperatures or those requiring less energy-intensive processing contributes significantly to overall energy savings. This nuanced material selection approach aims to strike a balance between sustainability, product quality, and process efficiency, reinforcing the extrusion process's environmental responsibility.
WEBER 107MM Flat Twin Screw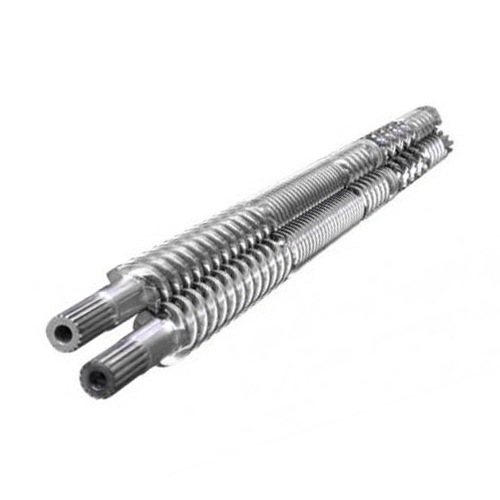