What safety features or mechanisms are typically incorporated into conical twin screw barrels to prevent issues such as overheating or blockages?
Several safety features and mechanisms are commonly incorporated into conical twin screw barrels to prevent issues such as overheating or blockages. These features are designed to ensure the reliable and safe operation of the equipment. Some typical safety measures include:
Temperature Monitoring and Control:
Temperature Sensors: Utilizing high-precision thermocouples or infrared sensors, temperature is continuously monitored at multiple points along the conical twin screw barrel.
PLC-Controlled Systems: Programmable Logic Controllers (PLCs) or sophisticated control systems dynamically adjust the barrel's heating or cooling elements based on real-time temperature data, ensuring precise thermal management.
Pressure Monitoring:
Strategically Placed Pressure Transducers: Pressure transducers are strategically positioned at critical junctures within the barrel to provide accurate pressure readings.
Integrated Alarm Systems: In the event of abnormal pressure fluctuations, integrated alarm systems activate, providing both audible and visual warnings. Automated adjustments to processing parameters can also be initiated to mitigate pressure-related risks.
Emergency Stop (E-stop) Systems:
Redundant E-stop Devices: Multiple emergency stop devices, featuring redundant systems, are strategically placed for rapid access, allowing operators to instantly halt operations in emergencies or unsafe conditions.
Torque Limiting:
Precision Torque Sensors: Utilizing advanced torque sensors, the conical twin screw barrel measures torque with high precision.
Mechanical Overload Protection: Automatic torque limiting mechanisms engage swiftly if the measured torque surpasses predetermined thresholds, preventing mechanical overload and potential damage.
Reverse Rotation Prevention:
Directional Control Locks: Mechanical or electronic locks ensure unidirectional rotation, safeguarding against any inadvertent reverse rotation that could lead to material blockages or operational disruptions.
Cooling Systems:
High-Efficiency Cooling Jackets: Employing advanced cooling jackets or heat exchangers, the system dissipates excess heat efficiently.
Closed-Loop Cooling: Closed-loop cooling systems maintain optimal temperatures, preventing overheating and guaranteeing the integrity of processed materials.
Material Feed Control:
Automated Material Feeders: Sophisticated material feed systems, regulated by sensors and controllers, automate the rate of material delivery into the barrel.
Smart Feed Algorithms: Intelligent algorithms ensure a consistent material flow, mitigating the risk of overloading and enhancing the overall processing uniformity.
Automatic Lubrication Systems:
Precision Lubrication Pumps: Automated lubrication pumps deliver controlled amounts of lubricant to critical components, minimizing friction and wear.
Scheduled Lubrication Cycles: Scheduled lubrication cycles ensure that components receive regular, optimal lubrication, enhancing operational efficiency and longevity.
Barrel Inspection Windows:
Durable Transparent Windows: Constructed from robust transparent materials, inspection windows provide operators with a clear view inside the barrel.
Quick-Release Mechanisms: Some systems feature quick-release mechanisms for easy removal of inspection windows, facilitating swift and thorough visual inspections for signs of wear, degradation, or irregularities.
Alarm Systems:
Customizable Alarms: Alarms are customizable to specific parameters, offering a range of audible and visual alerts. This customization allows operators to tailor the alarm system to their specific operational needs.
Remote Monitoring: In advanced systems, alarms may be integrated with remote monitoring capabilities, enabling operators to receive alerts and monitor system status from a centralized control station.
Conical twin screw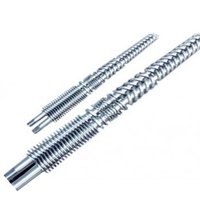