What are the key differences in output rates between conical twin screw barrels and other extrusion equipment?
The key differences in output rates between conical twin screw barrels and other extrusion equipment primarily revolve around their design, processing capabilities, and efficiency. Here are some points of comparison:
Processing Efficiency: Conical twin screw barrels represent a pinnacle of processing efficiency in extrusion technology. Their design harnesses the mechanical advantage of two intermeshing screws working in tandem, creating a dynamic environment where materials are subjected to intense shear, compression, and mixing forces. This efficient utilization of mechanical energy ensures that materials are processed swiftly and thoroughly, resulting in minimal energy wastage and maximum output per unit of time.
Throughput: The throughput capacity of conical twin screw barrels is unmatched by many other extrusion systems. This is attributable to their unique screw geometry, which optimizes material flow and residence time within the barrel. The intermeshing screws continuously transport material forward while imparting sufficient shear and thermal energy to melt and homogenize the feedstock rapidly. As a result, conical twin screw barrels can sustain high processing speeds without compromising on product quality or consistency, making them indispensable for high-volume manufacturing operations.
Material Flexibility: One of the most compelling advantages of conical twin screw barrels is their unparalleled versatility in processing a vast array of materials. From commodity plastics to engineering polymers, elastomers, and even recycled or filled compounds, conical twin screw barrels can handle them all with equal proficiency. This versatility is owed to their ability to accommodate varying screw configurations, barrel heating and cooling zones, and process parameters, allowing users to tailor the extrusion process to suit the specific requirements of each material formulation.
Melt Quality: Quality is non-negotiable in modern manufacturing, and conical twin screw barrels deliver on this front with unwavering precision. By virtue of their exceptional mixing and dispersion capabilities, these extruders ensure that additives, fillers, and pigments are uniformly distributed throughout the melt, resulting in products of unparalleled consistency and performance. Whether it's achieving precise color matching, enhancing mechanical properties, or imparting specialty functionalities, conical twin screw barrels are the go-to choice for manufacturers who demand nothing short of perfection in their end products.
Energy Consumption: In an era where sustainability is paramount, conical twin screw barrels emerge as champions of energy efficiency. While their initial energy requirements may appear substantial, they more than compensate for it through their superior processing efficiency and reduced energy consumption per unit of output. By minimizing energy losses and optimizing thermal management, these extruders help manufacturers slash operating costs, mitigate environmental impact, and uphold their commitment to sustainable production practices.
Size and Scale: Whether you're a small-scale boutique operation or a multinational conglomerate, conical twin screw barrels offer a scalable solution that grows with your business. With a diverse range of sizes, configurations, and accessories to choose from, users can customize their extrusion setup to match their specific production requirements and space constraints. This scalability ensures that manufacturers can expand their capacity, diversify their product portfolio, or enter new markets with confidence, knowing that their extrusion equipment can keep pace with their ambitions.
Conical twin screw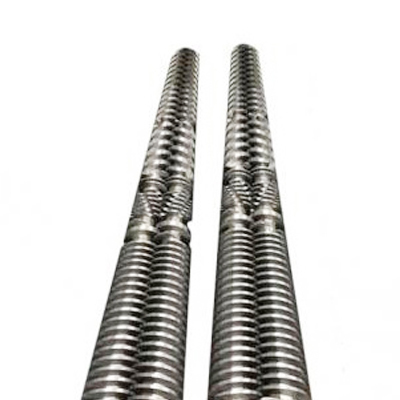